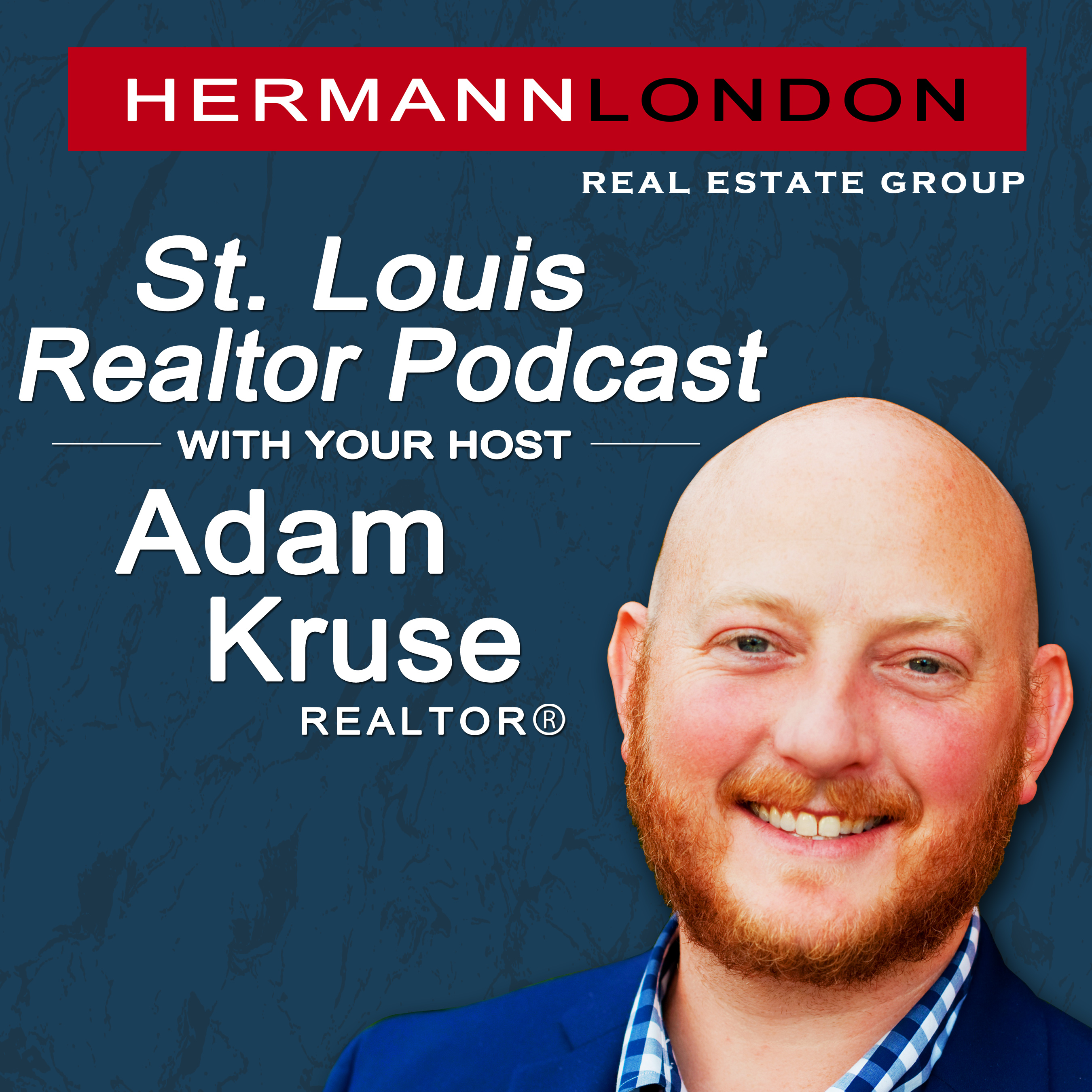
31 Oct Ep. 48 A Conversation at a Coffeehouse About Shipping Container Homes
In this episode, Realtor Adam Kruse and Realtor Shannon St. Pierre talk shipping container homes with Zachary Smithey and Joseph Bandalos at La Mancha Coffeehouse right down the street from the shipping container house they are building in Old North St. Louis
Email questions to PODCAST@HermannLondon.com
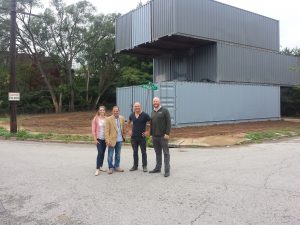
Shanon St. Pierre, Zachary Smithey, Joseph Bandalos, and Adam Kruse
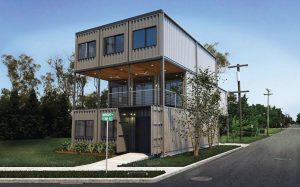
Rendering of front of the shipping container home Zachary Smithey and Joseph Bandalos are building in Old North St. Louis
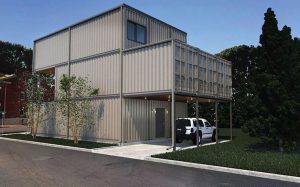
Rendering of back of the shipping container home Zachary Smithey and Joseph Bandalos are building in Old North St. Louis
WHAT’S INSIDE
0:30 Adam and Shannon are live from La Mancha Coffeehouse across from Crown Candy talking to Zack Smithe and Joseph Bandelos
1:00 Zack and Joseph are building a shipping container home in Old North St. Louis
1:14 Joseph Bandelos caused some controversy when he built a shipping container home in St. Charles
1:28 Why build shipping container homes?
1:46 Is it cheaper to buy shipping containers?
2:20 Are there a ton of shipping containers available to buy?
2:41 When is a shipping container taken out of circulation?
3:26 Is it hard to turn a shipping container into scrap metal?
4:30 What was the approval process like?
6:06 What is involved with maintaining the structural integrity?
6:51 How many square feet is one container?
7:18 Is a foundation required even for a tiny home shipping container? Does it have to be on wheels?
7:52 How do you make a shipping container permanent?
8:15 How can stacking shipping containers make natural decks and carports? How high can you stack shipping containers?
9:27 Contact information Zachary.smithey@gmail.com, jbandalos@hotmail.com
10:21 Zach is working on efficient designs for affordable housing
10:31 The owner of the property who is having the shipping container built in Old North bought the land from the LRA
11:29 What kind of foundation was poured for the Old North shipping container home?
13:28 Can a shipping container house be blown away?
13:55 Adam wants a shipping container home on his property in Steelville. How hard is it to cut holes in the walls of a shipping container?
15:30 How do the overhanging parts of the shipping container home work?
16:20 How much welding is needed on a shipping container house?
18:20 The Old North shipping container home will be made up of 9 containers and be 2,800 square feet with 3 bed and 2.5 baths.
18:50 How hard was it to get a shipping container home financed by a bank? Why did the banks not want the home build in Old North?
20:15 Getting comps after more shipping container homes are built
20:30 A shipping container home often becomes a destination after it is built. Strangers take pictures and knock on the doors.
21:45 What is the general cost for an empty container? How much does it cost to prepare a container for a home?
23:10 What is the average worth per square foot of a finished shipping container home?
23:30 Did any other shipping container homes inspire the design of Zach’s house? What is the most challenging part of building a shipping container home?
25:15 What kind of floor does the shipping container come with? Why are pesticides used on the floors of a shipping container?
26:45 What are the different levels of conditions of shipping containers?
27:48 How do you make a shipping container rust proof and how do you paint it?
28:45 What has been the process of customizing the Old North home? How do you make exposed ducts and conduit look pleasing?
33:25 Is a shipping container home tornado resistant?
35:00 Do you have to add any pitch to a shipping container’s flat roof?
36:40 How will the next shipping container home be different?
39:10 The Old North house should be done in January/February
TRANSCRIPTION
Adam: five from the rooftop of the Herman London real estate group in beautiful downtown Maplewood it’s the st. Louis realtor podcast with your host Adam Kruse welcome welcome everybody to the st. Louis realtor podcast live today actually from La Mancha coffee shop in Old North st. Louis right across from crown candy I’m here with Shannon st. Pierre my co-host
Shannon: hello
Adam: and we have two very special guests today you may have heard of them Zachary Smithey am I saying that right
Zach: yes
Adam: okay and Joseph Bandalos
Joseph: correct
Adam: and we are here to talk about container homes today you guys are building this amazing looking three-story super interesting architectural container home here in old (2) North right
Joseph: yes
Adam: and Zach people may have heard of you because you’re the guy who built the container home in st. Charles
Zach: yep yeah caused quite a controversy which I didn’t think it would
Shannon: well stir and a few more ordinances that they have in place now
Adam: okay so that’s kind of just I just have a couple overview questions so tell me why container homes
Zach: for me personally when I was building my house it was about saving money so it was economic but it was also about recycling repurposing and sustainable building
Adam: okay so it is it economic I mean buying these container homes is they’re fairly cheap to buy I guess and
Zach: yes it can be economic so for design you get it is usually cheaper than standard construction but sometimes you see these really outrageous designs and people like oh well that’s not except that’s not any cheaper than normal construction but you’re getting a very exotic design so if you go with the more simple design yes it’s much cheaper than standard construction
Adam: okay
Zach: it all depends on the design
Adam: are there are tons of these containers shipping containers just available around the world in the country
Zach: oh yeah there are approximately 34 million on the planet and most of them are beyond their (2) years and they’re continually being built
Adam: so they (2) build it they use it for a while to ship whatever around the world and then how do they decide when to stop using it
Zach: you know I’m not sure if they have just a usage or a time line or just the general construction
Joseph: they have a requirement to have the new watches seaworthiness or standing up so has them has a specific test if it doesn’t pass that test and it has to be brought up to standards and if it’s not for the pass and if it’s taken off a lot yeah I’ll take it out of circulation
Shannon: okay and then what did they do with them back no then
Joseph: he’ll just be stored then they’ll have yards of them where they’ll just sell them off and do what either what we’re doing or just sell them for this [???]
Shannon: do you scrap them
Joseph: Yeah is [???]
Shannon: [???] reuse [???]
Joseph: not really that much and there’s just too many of them to be doing that but they try they try to get more use out of them than just a scrap metal
Zach: and as far as scrap metal a containers built in such a way that you have to put more energy into cutting it down to scrap it then it’s worth they’re going to get back out of it
Adam: so let me back up for a minute Jack you’re (3) the guy who originally thought of doing this locally right and what is your role in this home that we toured today
Shannon: here an old not
Zach: yes I I spent the year in two weeks building mine from scratch I’m designing it because the bank wouldn’t give me loan I decided I didn’t want to spend another year building this one so I was on the design and consulting side
Adam: okay (2) and Joseph you obviously you’re the general contractor
Joseph: correct
Adam: but you seem to know a lot about shipping containers is this your first
Joseph: I’m shipping container project I’ve been involved with shipping containers in the past in commercial sides as well as how to apply we have a design on a particular ship in famous to making collapsible so I’ve had I worked with them internationally as well so I have a fair share of experience with shipping pens
Adam: Wow okay well so what was the process that you guys had to go through to get the approval to build this home you know and part of the reason I asked that because I think people that are seeing your photos online already are probably reaching out to you guys when I want one you know and I know I’m driving around seeing a vacant lifestyle post or a vacant lot in Midwood today and I’m going we need a 70 dinner home there right
Zach: yeah
Adam: what’s the process
Zach: every municipality is different so every city every neighborhood is different luckily the city of st. Louis is very accommodating they want progress they want people to come in and do interesting things
Adam: is that by alderman or is that just the entire city of st. Louis it’s probably going to be approved
Zach: Jill might know
Joseph: as far as the city that are Ralph’s at the plane club and very welcoming and very supportive with the project and you know with us meeting the guidelines of the architects approvals and plans are they’ve been very supportive with giving us what we needed to do
Adam: I mean I’m guessing that the approval has nothing to do with like two strengths or the structural integrity of it these are strong buildings right if you’re about aesthetics or whether
Joseph: negative there’s a lot of structure that goes involved if that gets put in as well because when you start stacking them there’s a lot of structural you know climates that needs to be met there which supports you just take it because remember wind still plays a part of all of this where they can get either blown over you know a base (2) they hold as far as structural strength they hold a lot but you still have to make sure to put together properly in order for them to have that strength
Zach: and that goes back to the design that we were talking about and design costs construction costs based on design in Travis’s construction we’re cutting out almost all of the interior walls
Adam: and that was Travis to a guy who you’re building the home port
Zach: yes
Adam: okay
Zach: and when you do that most of the structural integrity of containers in the walls so then you have to put in I beams and other posts to take that low
Adam: okay so you guys had to get structural engineers involved and kind of planning all this stuff
Zach: yes very much structure luckily his design as far as the interior goes is very similar to mine so we already went through this process once okay
Adam: so how many square feet is each container
Zach: 320 square feet
Adam: Wow okay so you could someone could probably just use one and make it their house
Zach: yeah that’s a large that’s on the larger side of a tiny home
Adam: uh-huh I mean has people reaching out to you asking for kind of thing yet or
Zach: yes and I haven’t had time to go through all of those requests but I have a list
Adam: you do okay it’s
Shannon: now we do you have to build a foundation for even just a single
Zach: as well so if you zone it as a tiny home it has to be on wheels it has to be mobile
Shannon: okay
Zach: but if you want it on a lot then you run into certain problems where a city wants it to be a minimum square feet which would probably be two containers 640 square feet depending on what the city requirements for the minimum square footages
Shannon: you know what the code is to
Joseph: know on many requirements I’m not sure what the code is on the neutron bomb to answer your question as well to make a permanent Peppa at least put them on a peg so you don’t have to have a foundation to each one but as long as there’s a flat
Shannon: slab
Joseph: slab we could we could run a patent and join the back way
Adam: it’s so cool like what you’ve done with this house where there you know there’s two sitting next to each other there’s three sitting there together and then there the next layer is back so then you get this supercool like VIP deck from the second layer right and then on the back of it you get sort of a cover and this guy’s going to use a carport you say
Zach: yes it has a 13 foot cantilever the center floor is pushed back 13 feet the first thing third floors are directly above each other
Adam: okay is there any idea how many of these we could stack on top of each other
Zach: these can go I believe 10 high fully loaded with 60,000 pounds of each when they’re on a container ship so when they’re fully loaded not (2) even counting like as a house so I’m not really sure it depends on how much or the wall structure you cut out you can go at least 10 stories tall
Adam: I mean everyone goes now where looks at City are we done Abu Dhabi
Zach: Dubai
Adam: Dubai everyone go signify to see like the super interesting architecture I think the next thing here is Joseph and Zach are gonna build a 100 story tall
[???]
Shannon: yeah, I think you should just do that for engineering team like yes for fine
Zach: oh yeah I’m intuitive if anybody’s out there who wants to pair up with us let’s get it done
Adam: yeah by the way I do want people to be able to reach out to you if they if you want them to
Zach: yes
Adam: so do you want to give any sort of contact information for people this thing
Zach: yes you can send me an email at Zachary.smithey@gmail.com and that’s Zachary.smithey@gmail.com
Joseph: and mine is for the construction site is Joseph Bandalos that’s jbandalos@hotmail.com
Adam: so that’s jbandalos@hotmail.com
Joseph: correct
Adam: ok cool because I know people that are listening are gonna want to reach out together and hopefully some of them will do business with dudes a lot of them will just have questions and want to record podcast
Zach: and another thing that I’m working on right now are very efficient designs using this type of construction so we can bring construction costs down for a horrible housing in st. Louis which I think there’s a huge need for
Adam: okay so let’s talk about this one that we just toured all right
Zach: yes
Adam: did he buy the lot did you sit then I read that he bought the lot from the LRA
Zach: yes
Adam: okay
Shannon: it’s a pretty sweet lot
Zach: it’s a large lot yeah
Shannon: that’s a very large lot but it’s a corner lot that his dad that second-story deck that with his master suite world now overlook the arch
Zach: yes right down the end of the street really easy in the arc
Shannon: yes it’s an amazing Street and laminates arch at the very end of Prague and framed I mean it’s cool
Adam: the interviews Laura from the LRA a few podcasts ago and I guess people can reach out to her they get a lot from her there’s a lot of them available right
Zach: yes
Shannon: we’re thinking of the LRA website too
Adam: okay so let me do you mind if I just run through a few more questions about the property this particular house itself what kind of foundation did you Court
Joseph: he was standing Foundation was our a crawlspace so it was a three foot high eight inch wall on top of our footing standing so it said pretty much but what made it very unique and different is constructing it and the cost exact that don’t want previously there was a lot of nuance there’s a lot of details that we were able to pay attention to that made it fall into place much easily a much easier than it would normally have a bomb without knowing these details especially what setting it into notches because the heads on containers they are at different levels and the bed’s meeting the feet when you stacking them they’re at different heights or the points the four corners they’re at different heights than the rails so when you’re stacking them can have spaces and gaps in between these containers that really would not be expected thinking that they’re flush with the rest of the container and they’re not so knowing these details and ahead of time it made it much easier for us to put these in place in a single afternoon [???]
Zach: and we embedded steel plates into the foundation around the perimeter and where the feet land as well so when we Trump these metal containers you have these embedded anchored plates that we’ve well containers to Isis a welded down
Adam: yeah I saw they were welding the container to that sort of I guess you’re calling in a plate but how is the plate connected to the concrete foundation
Joseph: that’s held with interior will I clips I hooks and inside the plates that are welded which are on all the plates which are on the angle iron plates as well as the base plates that sit underneath the feet themselves
Shannon: and is that drilled into the foundation
Joseph: it’s actually when it’s board it’s placed in the foundation as me where that’s placed in as a core so that’s where the details come in when pouring the foundation
Adam: and every here everything that would have hopes with the wind ruthless
Joseph: well when you say when proofing is G actually actually helps with the weather proofing totally is now the container is sitting directly on the plates exactly just mentioning without any gaps or Aldi’s and then it gets welded directly to the plate all full airspace
Zach: yeah whereas a normal house is not anchored down to the foundation is basically sitting on it so this can’t get blown away it’s anchored water
Joseph: right
Adam: okay so you know I’ve been really interested in shipping container homes and things like that for a while I have like a little piece of land down by sea level and I want to put a sippy container they’re like secure my stuff basically and when I watch all these YouTube videos one of the things I find is they all complain about how hard it is to cut the holes in the wall and they’re using a thousand grinder wheels or whatever is there a better way have you guys found a better way to cut the holes or is it dried in a mouth
Joseph: no grinding is (2) one way it’s more precise but it’s much more time-consuming and you can use a lot more consumables the materials we have a plasma cutter which is more expensive initially but then it’s less expensive on a long run because so using less of consumables that you do with the blades and also then just a regular to be using of torches it’s much more slag involved and a lot more a lot less detail
Adam: so you’re using a plasma cutter and you’re saying it’s not as fine of a detail but when you’re cutting the entire wall out because with that less important
Zach: it doesn’t matter
Joseph: right
Zach: will you will be using the grinder blade or doors and windows they have that flush straight line precise card
Shannon: exact you back there what 200 and how many
Zach: yeah at least 200 grinder blades
Shannon: per head
Zach: yeah and you know it’s (2) something that you learned and I was on a time schedule so yeah just went with it
Adam: it’s kind of dangerous because kiddos great are those
Zach: yeah if you get them in a bind they’ll shatter and it’ll throw stuff at you
Adam: are you guys wearing you got your guys wearing also the safety protection all that separately
Zach: yes
Adam: it’s so for the interesting sort of kind of cantilever what it was called a design of this house but
Zach: it is a cantilever but we will have posts so it’s not a true cantilever it won’t be hanging very light so
Joseph: it’s just an overhanging 13 foot overhang
Adam: okay
Joseph: and then and then that 1308 put overhang on the second floors compensated by the next containment up to 13 and foot overhang country setting back to the original container itself
Adam: I noticed you guys have guys that are today they were doing all sorts of welding it seems like you had to add a ton of extra supporting beams holding them up and you said that
Joseph: right not extra I mean it’s all it was all calculated just it’s a massive amount of welding involving the amount of when you’re building a house I mean all of it really is not so much realize because it’s wood and you know you’re just cutting board and now I get together here it’s the same thing but there’s a lot more steel involving because it’s a metal place or metal facility you know it’s just a lot more welders involved
Shannon: and so do you have to put the beams on and place or are you
Zach: most of the beams we set so the beams that go in between the containers
Shannon: yeah
Zach: so we said container (2) then drop the beam in between and we said another container dropped another beam some of the exterior beams that hold up like the overhanging
Shannon: yeah
Zach: we put in later
Joseph: those i-beams again when we talk about preparation you know Zach and I were able to place nine containers in a single afternoon anomaly just mean an afternoon in a full day work we started at seven o’clock had the first container arrived at 7:30 we were placed in the first one by 8 o’clock and we were wrapping up in the kitchen the crane was going out of there by 8:30 so we were only able to do that and that was when a full lunch as well lunch time lunch break but we were only able to do that with all the preparation where supply beams that have to go into place does it begin a lot more preparation it’s not just dropping ivy you know the i-beams are actually prepared with a top plate that gets welded to the i-beam and that that top plate has to get free with notches and cutouts so that when they get put into place it’s all going into place like a Lego system
Shannon: it’s pretty cool
Zach: and this design I mean this is more of an exotic designs more on the higher-end designs for container home we’re still coming in at about $100 a square foot so I mean traditional this is construction distance
Shannon: away claire
Zach: yeah traditional construction you’ve pretty much started a hundred for base and go up from there so he’s at the higher end of design and still at the base of traditional costs
Adam: and he’s gonna have a big
Zach: yeah
Shannon: how many per sqft
Zach: twenty eight hundred and eighty square feet for nineteen containers
Shannon: and [???] I think what was interesting so you did not to get along for your home the bank wouldn’t allow it probably particularly put it in a certain category however Travis is doing a bank loan abuse okay but there are requirements which
Zach: yes
Shannon: now how many bedrooms about is yours
Zach: Mine is three bad and two and a half baths
Shannon: okay and this is and required to be a minimum of three beds two baths
Zach: yes
Shannon: today the left
Zach: and he’s got three bed to nap bath he only wanted one bedroom but the bank wouldn’t allow that for resale value purposes so on the third floor he put the minimum requirement of two tiny bedrooms and another bathroom
Adam: do you want to mention what bank who’s able to work with who do you think mini bank should be
Shannon: did he go did he have to go to do a lot of things
Zach: he did go through a lot of banks and it wasn’t just the (2) difficulty of getting the loan because it’s a container home but then he also had to deal with redlining because of the area that he’s constructing in it so dividing to redline in him because of this is an old know and several banks told them you have the credit we would loan to you but can you build it somewhere else and they didn’t want to build you know
Adam: Realtors aren’t allowed to do redlining I guess maybe banks are
Zach: I don’t think they’re supposed to but
Shannon: well doesn’t come out to my it’s a evaluation and being able to
Zach: comparables in action here on your [???]
Shannon: just in case there’s a default on the block so I think that they have some guidelines
Zach: and then one thing that should be getting easier for container homes not counting redlining is that the more we build the more comparables that we’re building like this might have been easier because mine was already built and they’re very similar in size Brooke and the next one should be even easy
Joseph: will be nice is now this will set a precedent for comps so now that we can now that we have this and when this one’s completed we’ll have a nice calm we won’t be able to have a community so people will be able to fly into the dome or wherever they’re visiting or a Convention Center helps them to do at night and drive by you have some of the ground can do Lamantia and they don’t have a breakfast or lunch or don’t we sit to contain two home districts
Zach: yeah
Joseph: I hope to have the container home district
Zach: I’m sure that this is gonna be a destination his house
Shannon: it already is [???]
Zach: yeah right I mean I still have people driving by mine daily and stopping and taking pictures and almost weekly somebody will knock on the door and ask questions get out of here right and
Shannon: here my question is asking this point
Zach: some of them are dumb questions like is this insane your home is on TV but most of them are really just concerned with like how did you do it like how did you get approval can I do this can you do this for me
Shannon: you like those door mat [???]
Zach: right yeah I have to screen a lot of them because then they’re thinking hey what can I build for forty thousand
Shannon: like a tiny house [???]
Zach: hey yeah well they’re thinking bigger than tiny home and I have to break it to him then we’re gonna have to go tiny for that price
Adam: well speaking of that so each container I guess dependent depends on the size of the container the condition is there like a general cost per contained raw container
Joseph: what is a question
Adam: is there a kind of a general cost per I guess it’s a 40-foot because use the nine foot tall was a direction like you is there kind of a general cost for that you can give to people
Joseph: um for the continued to purchase two container for a square foot to complete it that’s
Adam: the purchase the container
Joseph: purchase the container as we were talking you’re looking at about right now between twenty to fifty to twenty five hundred dollars per container but the course of God you know the price increasing steel at all and the top three in container companies merging the container purchasing and containers have changed a lot and certainly in the past three to six months so there is a lot more work involved with the containers so although you may be getting a good price on them you really have to consider and weigh is it worth my time and effort involved preparing the container for the condition in which I want to have it look as a home I want to just purchase a new container I just have to drop into place
Adam: okay
Joseph: new containers are going to range anywhere from around they start at $5,500 so the difference and take into consideration by the time you’re looking at tax and delivery and all that take into consideration that’s not just 20 to 50 to 500 container Hey you’re looking at approximately thirty five hundred dollars per container
Shannon: okay
Zach: and you guys mentioned roughly around $100 a square foot for this particular property but I guess every house would be different depending on what the people want and all that stuff right they seem to reach out to you and not (2) just use that as a set number
Joseph: correctly
Zach: okay
Shannon: now we’re there other container homes around the country that did you quality went out when you yours and get any advice to try and learn or we like that I’m just gonna do it
Zach: yeah I mean I’m a professional artist and so I just looked at this like a giant sculpture and whereas normal construction and I’ve renovated several homes in the past normal construction is an additive process you build it from the ground up you’re just adding things this you stack everything up in a day then it becomes a subtractive process where you’re removing things then it becomes an additive process again so it’s it’s basically it’s just a giant sculpture and I just like figuring things out as I go
Shannon: okay so when you were doing yours what was the single most difficult project I mean they’re all challenging again
Zach: yeah
Shannon: and they’re gonna write the single most challenging
Zach: physically considering it didn’t have a crew helping me cutting and removing the walls was really really physically difficult the walls are really heavy that’s really heavy steel so cutting those out and then carrying them out of the house in six foot by four foot eight foot by four foot sections they’re around 180 200 pounds each and sharp so
Shannon: so how I stayed in shape
Zach: yeah well that’s how I stayed in shape that here
Adam: I guess if you cut the whole wall up [???] again and then go home
Zach: yeah oh yes so my first few cuts were just trying to figure out like what size is manageable is I didn’t really have an idea how much each section was gonna
Adam: let wish you knew Joseph then and he could have brought over his plasma cutter
Zach: yes (2)
Adam: so in these in these properties containers they seem like they come with the wood floor
Zach: they deal one-inch-thick hardwood plywood
Adam: 1 inch thick hardwood plywood and at that part of the deal is you gotta find a container that has the floor to give shape
Zach: from what I’ve seen all the ones I’ve seen have decent floors
Shannon: just shaking his hat so[???]
Zach: some of them that have neat prep I mean some of them are you know they can be split a little bit I haven’t seen any with bad holes that are workable but if you have a oil spill on there you’re gonna have to sand that up but where you can lay down anything on top
Adam: and you when we were doing the tour can you tell just tell everyone again what you said about they had some sort of bug spray on
Zach: yeah they’re sealed with a pesticide
Shannon: the floors themselves because they are wood
Zach: yes it’s the only part that bugs could eat so they’re sealed with a pesticide so they say if you’re gonna use this for a home either seal it in or get rid of it so I chose to seal them in with a two-part epoxy mixture
Adam: from that perspective would it be okay to sand them or breathing in all this stuff
Zach: I well yet wear a respirator if you’re gonna sand those floors and then even if that still seal them up
Adam: and anyway please contact the drill press
Zach: and yeah and like what Joe is shaking his head no he’s seen a lot of rough container floors when you’re ordering these containers you can order them with an inspection
Shannon: so you were dough is nothing about levels so there’s different levels of conditions they can healer actually exchange older tests
Joseph: in the past three to four months by the time the executive containers was an ideal time and any time left it all the best three to four months ago it was really time to buy now they’re taking a lot out of circulation so they’re trying to eliminate a lot of those all the ones and it was very time-consuming for me just even pick out the nine that we had picked out to get ones that were acceptable to be livable without so much damage but yeah it is (2) a good amount of work that I have I had with either bird heavy burn marks gouges there’s some areas that they’re gonna have to be addressed
Shannon: I think that’s part of the charm your daughter’s jeans and the dents I saw on the walls and there it was Sunday in containers
Joseph: it’s what gives it the trauma of that’s the purpose of living in that type of you know eclectic orchids it’s nice it’s what you make out of it and to me that’s part the chomp
Zach: yeah well its recycling whether to show up
Adam: does you have to use some sort of special kind of paint to make it like rust proof and
Zach: so any rough spots we seal with an epoxy and then after that leaves a DTM direct to metal thing
Adam: okay
Zach: which I guess is good for the flexing the expansion and contraction of metal right
Joseph: we what we what we’ve done is working exactly just so we put the epoxy on on the bare metal area is a two-part epoxy to prevent any future rust or anything or actually from spreading and then we put a fun the whole containers would apply mark DTM primer and on top of the properly put the final coat
Adam: and how long from now do you think Travis will have to repaint it is
[???]
Shannon: so the colors will go out of fashion before he needs to be right
Zach: yeah
Adam: as you guys are going through this with this particular guide Travis what is the process been about getting his input on the layout and the finishes versus what you already have from your experience you know what’s the kind of process going to look like someone who wants to call you
Joseph: well working with Travis again has actually been a pleasure I really call the clients and customers and hormones that I’ve worked with they’ve been the most understanding and comfortable people to work with and not because they’re just easygoing they’re understandable so they put a lot of logic behind it they’re very methodical they know what they want they know the decisions and when I explained something to them with a reasonable understanding you know they’re very willing to understand the differences and very easy very easy to work
Shannon: well I think is some way as you say that I think traditionally in our mindsets when we build a house we want all these things new granite countertops and stainless steel appliances but when I start thinking about outfitting a container home I feel like there’s zero expectation because it’s not type of home that kind of exists on the mainstream so it’s kind of like a wide open canvas though
Joseph: yes I know my concern is that when you get somebody like that you have to have an open mind to be an eclectic into what you want to have it to look at and the outcome remember these containers are used so there’s dense so if somebody was so neurotic to say well if I’m going to fix these decks I want to perfectly not going to because that’s part of right that’s part of what you want to I know so unless you want to go with that extra expense so they’re very understanding is what I should say
Shannon: so how will they be outfitting this one is this new materials is it like yours recycled is it a mix of the two of these
Zach: [???] as eclectic is my house
Shannon: like history [???]
Adam: dry walled and stop her
Zach: yes all of them so we have to insulate the all of the exterior walls frame and then drywall
Adam: okay because you know so my dad built a new home 20 years ago whatever and I just remember him getting into the detail to build already had the plans you know they built the same home a hundred times already or whatever and he’s like well I don’t want this outlet here I want it like toe foot are 12 inches to the right you know and I’m kind of thinking you know you probably don’t want to work with my dad as a client on your container home my dad’s awesome though by the way but you kind of get into that layer of detail with somebody like this because this is the first container home with this design right
Zach: we have done some redesigns on the interior walls and like trying to figure out where the ductwork is going to go where the electric is and the is gonna be run so we had to move some walls a few inches we had to go over some of those details but I think in general like we were talking earlier they’re open to you know the ideas of let’s just make this functional and my hair
Joseph: I think we got a lot of synergy between the three or four that I wanna say three of us put the three groups meeting on Travis and Gina and Zach and myself you know with them being the final decision Gina and Travis and with the brainstorming of Zach with the three of us putting our heads together or whenever we come up against it I don’t to say dilemma but you know some decision-making we’ve had very I feel good synergy as to how we want the outcome to be
Zach: and in the very beginning I explained some of the things that they should be open to and expect such as in certain areas you’re going to have exposed electrical conduit or exposed ductwork
Shannon:we think that that would fit right in with me
Zach: yeah it’s just a part it’s a design answer that thing yeah
Joseph: yes and no I and (2) here’s why – because you’re only working with you know nine foot ceilings it’s not like you’re working with the loft downtown where you have the 14-foot ceilings so when you do put that open ductwork now you’re gonna impede from a nine-foot ceiling which is what you’re looking for you’re going for all IQ now it drops it down to eat or maybe even less so really where we gonna put the ductwork to make it look as the most aesthetically pleasing and then the conduit how do we do that because understand what this – we’re working with original and I say original we’re working with the original walls and ceilings there’s no sheetrock on the ceiling so these this conduit now has to be exposed so we want it to be the most pleasing to the eye as well and you want to have it you know in a manner that’s comfortable and women like
Shannon: okay
Adam: so this is a like you were talking about when we were there this would be a great place to be if there was a tornado seems like a good place to be if there was a zombie attack you know
Joseph: he needs to decide who his friends on yeah mister [???]
Adam; yeah I recently my buddy got me all paranoid and I’m into this whole like in today’s thing and I’ve started buying food and it’s in my basement all the stuff a shipping container home seems like the perfect place to go
Zach: oh yeah definitely and as far as tornado-proof this entire home is a storm shelter well everything being welded to everything else you should just be worried about not being next to a window
Adam: because you’re gonna cut windows out obviously and so I kept thinking oh man you could just close those doors but then he’ll still have windows and you’re probably not gonna have maybe like in the future do you think when you cut the window out you would keep that metal and make it so you can like is that just yeah is that just ridiculous that
Zach: I think it would just be unnecessary if if you ever reached that conclusion I guess you could just nail some plywood to the interior cover him up
Joseph: he’s gonna pack the car move
Zach: yeah
Joseph: but to answer your question it’s really different than what you’re thinking because what you’re saying is is can you use the doors as shutters not actually because the windows are not going to be on the sides of the doors the windows go on the back end that it contains where there’s no doors the only area where that would be is because then at that point you’d have to build the interior frame inside the door frame so we are doing that only at the front door level though every other window will be on the next area frame of the container nothing no windows will be cut out on any of the door areas
Shannon: okay that makes sense can I ask about the proof though because is it a true flat roof because it’s a container so it’s black like had it even on flat roofs here in the city we have pitch song pitch
Zach: you still have to have a pitch and we’re gonna go with the minimum eight inch drop for every 12
Shannon: so do you need to build up
Zach: [???] sorry now mine was a bitch so no every 12 inches
Shannon: well we’re richer well and just have the quarter inch drop is that the minimum standard and so are there is there any roofing materials or what are you how are you doing the roof
Zach: so is the roof
Shannon: routing of flat flat map
Zach: yeah (2) and that’s just the I mean that’s our basically the roof of the containers that’s our base roof on top of that we’ll build up foam insulation panels
Shannon: okay :
Zach: and that will also be the structure of the roof itself as well
Shannon: okay
Adam: so that’s about ten inches total from front to back right
Zach: we’re gonna go side to side
Joseph: correct
Adam: oh so I decide for so you’re saying on the roof you’re gonna build some little thing
Shannon: build it up
Zach: yeah it’ll be up on one side and slant towards the west side of the yard side
Joseph: correct
Adam: what’ll that be made other
Joseph: that’ll be the phone cord [???]
Adam: okay
Joseph: it’ll be a half a foot [???] slow it down
Zach: so what we have to get our art 30 years off of the roof
Adam: did you had an installation up there anyways so it’s like an insulated foam board to the altar elbow as the roof crazy
Joseph: okay and then it’ll be a flat TPO roof which is the [???]
[???]
Adam: awesome okay so as you guys have learned from this one you have a next big project booked or in your mind you have some new cool awesome idea that you’re going to do for the next one
Shannon: Oh what is the biggest change what do you learn you learn from yours you’re learning from this what are you gonna take them
Zach: efficiency is the idea for the next project I like the list of people who have contacted me I’ll dive into that list and see what’s best for the next project but right now I’m working on designs for a woman in Chicago and hers will be four containers two stories with a rooftop terrace
Joseph: what’s nice also you know it’s something with some of the designs you know Zach has taken blocks and we’ve sat him down at his studio and just went through some different creative ideas and you can take containers Nate but you can put them apart they don’t always have to be adjacent so if you said containers apart and just put a truss system one to the other you can start with two containers and yet have a structure that’s thousand sqft people by using the space in between as more ground footage or more area for to check you’re looking to have between
Adam: yeah [???] a v-shape one with something on top of that you know there’s all sorts of different so you’ve made like blocks that are sort of like a scale model size
Zach: yeah I’ve thought about to a 2 by 8 board I just measured how like that gives me the proportional width of the floor a 40-foot container then just measured where I need to make my cuts and I cut like hundreds of these blocks so I can just build models kind of look like giant Jenga
Adam: yeah you’ve seen like the 2×4 Jenga those bars now it’s kind of like that
Zach: yeah (2)
Adam: that’s awesome okay well anything else we want to say before we wrap it up
Shannon: so anything
Adam: let’s give your contact information one more time if you don’t mind
Zach: my email is Zachary.smithey@gmail.com you can also find me on Facebook or Instagram at Zachary Smithey
Joseph: mine is jbandalos@hotmail.com
Adam: we really appreciate you guys time today I know you got to get back to the house there’s a lot of work going on and maybe we’ll want to follow up with you again and you really don’t get it done and
Zach: we’re looking at four months
Adam: four months
Zach: so if you’d like to do another one in two months or so we’re gonna do a walk-through of the interior
Adam: yeah
Shannon: we good it is move-in date
Zach: we should perform four months from now
Joseph: look around Jen the middle of January to the end of gender again it’s a lot of it’s going to depend on whether at that time too I mean we’re trying to get as much as we can before the weather sets in so we’ve had a lot a lot of the delays now we’ll though we started we broke ground in July a lot of the issues that we had were pre-existing foundation issues and a lot of weather issues because of all the rain that we got this (2) summer
[???]
Adam: okay cool well thanks again for listening and thank you guys very much for letting us interview for our podcast and take care
Joseph: thank you